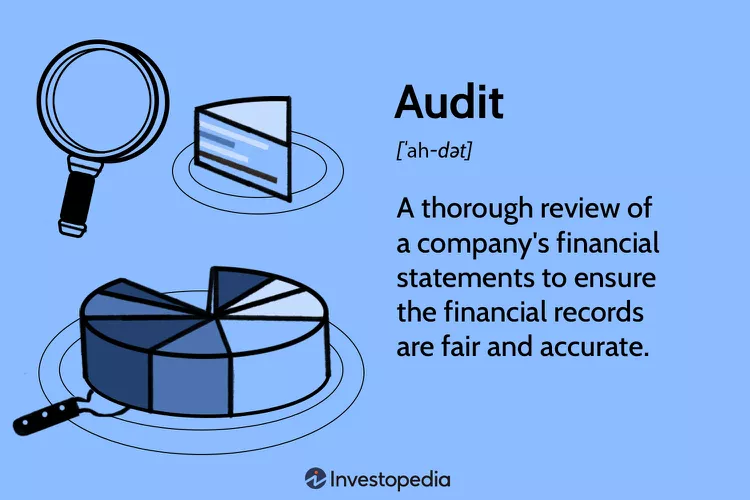
Loading...
In short, a Third Party Inspection (TPI) is an independent, unbiased group who inspects a manufacturing company’s key assets such as equipment, processes and heavy machinery. They confirm the compliance of these products, determining if they meet the legally-required international standards, codes and technical specifications.
No matter where you purchase equipment from, it must meet the same international standards. Even when you work with vendors from across the world, you have the responsibility of ensuring legal compliance.
By definition, these inspectors are literally a “third party” who take no part in the design, procurement, fabrication, construction or installation of the equipment — in other words, they have nothing to gain or lose from the results.
As Third Party Inspection is a necessary process for every manufacturing company, it’s important to ensure both quality and integrity in your chosen inspectors. Here, you’ll learn what factors are important when hiring your own Third Party Inspection company.
A local database of inspectors:-
Working with vendors located abroad can add an extra layer of complexity to the third party inspection process. It’s helpful to find a company who already has an international network and relationships with local and global third party inspection companies abroad. They already have a database of local inspectors, saving you the time of having to find them yourself in an unfamiliar place where you may not have many contacts.
ISO certification:-
The ISO9001 certification is an internationally-recognized credential that ensures the highest international quality and integrity in inspections. An ISO certified organisation will have a Quality Control System in place, which is followed, reviewed and updated to be in line with industrial changes. ISO-certified companies also have a system to conduct Internal Audits and strive for continuous improvement.
Since you choose your vendors based on selective production specifications, manufacturing compliance and expediting services, you need an inspector that’s verified and qualified for these same standards.
A company with a global network of third-party vendor inspectors:-
When dealing with international manufacturers, finding a global company who can serve as your single point of reference to access a worldwide network of offices and vendor inspection capabilities can expedite the process while saving you money. This way, they can service you in your own time zone, linking their local inspectors with your vendor — sparing you unnecessary time, travel and lodging expenses.
Companies that offer multiple services to save you time:-
When it comes to efficient vendor inspection, finding a company with all-in-one support packages can save a lot of time, effort and hassle. The best companies cover everything from source inspection, product assessment, vendor quality surveillance, compliance reports and expediting services, all coordinated in agreement with you.