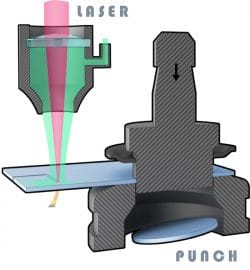
Loading...
By definition, sheet metal starts out flat, but before this, it comes from large cast ingot and the
rolled into a long ribbon in the desired thicknesses. These rolled coils are then flattened and sent as
large sheets cut to different lengths to accommodate the manufacturing shop’s needs. While this paper
focuses on bending sheet metal along a single axis, there are processes out there, hot and cold forming
techniques that include bending and forming sheet metal along multi-axis points in one process such as
deep drawing, hydroforming, spinning and stamping. These processes are most commonly found in the
manufacturing of products like automobile panels, aluminum cans, and complex formed consumer appliances.
Another similar process is progressive stamping which moves a ribbon along a series of stamping which
forms and punches different stages. At the end of these progressive stages, you are left with a finished
part.
Shearing was one of the longest standing means to cut sheet metal but has since been replaced by
faster, more precise methods.
Punch Press use tools called punch and dies, which punches holes and shapes to make any number
of patterns. Particularly effective for cutting simple patterns that are more economical than cutting on
a laser cutter or a water jet. Punch presses can operate at hundreds of strokes per minute making this a
suitable center for processing parts quickly.
Laser Cutting works with a combination of oxygen, nitrogen, helium, or carbon dioxide to burn away
material and produce a clean edge. This form of cutting can hold very tight tolerances.
Photochemical Machining is a process of controlling the etching using CAD-generated stencils to leave a
pattern that is chemically activated to remove unwanted material.
The edges of the sheet metal are folded over itself or folded over another piece of sheet metal in this
forming operation to achieve a tight fit or a stronger, rounded edge. Hemming is a technique to join
parts together, improve the appearance, or increase the strength and reinforce the edge of the part. Two
standard hemming processes include roll hemming and conventional die hemming. Roll hemming is carried
out incrementally with a hemming roller. An industrial robot guides the hemming roller and forms the
flange. Conventional die hemming is suitable for mass production. With die hemming, the flange is folded
over the entire length with a hemming tool.